Comment se fabrique un smartphone ? Visite chez un constructeur !
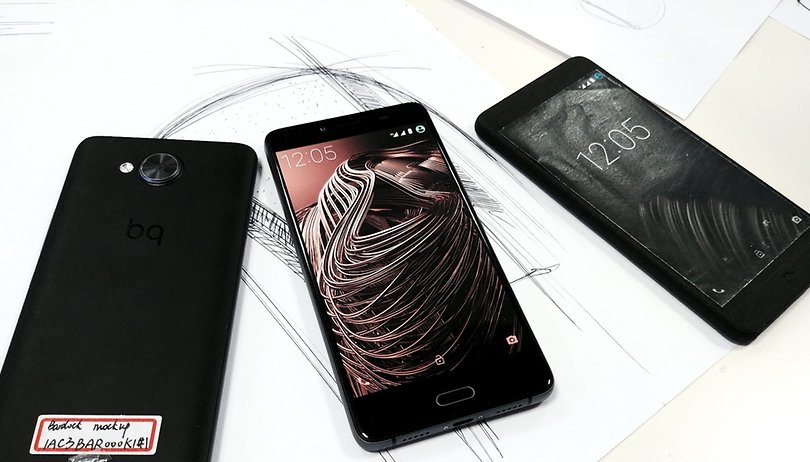
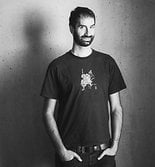
La plupart des smartphones ont un processus de développement et de conception très similaire qui fonctionne en cycle annuel. A partir du moment ou un smartphone est mis en vente jusqu'à ce que la prochaine génération sorte se déroule une course effrénée pour améliorer les performances et la conception de la génération précédente. Afin de vivre de près ce processus, nous nous sommes mis dans la peau de l'une des rares entreprises qui conçoivent des smartphones en Europe, BQ à Madrid.
Le processus d'élaboration d'un smartphone
L'industrie du smartphone fonctionne en cycles annuels. Chaque année, toutes les petites et grandes marques présentent leurs innovations et nouveaux modèles pour conquérir les utilisateurs et leur portefeuille. Si on enlève les présentations et préparations commerciales, il ne reste qu’environ 9 mois pour développer une nouvelle série de téléphones pour l'année suivante.
Il faut très bien contrôler les délais, et avoir une équipe de développeurs compétente chargée de mettre sur le marché un produit compétitif de qualité et performant. Voyons voir en détail ce processus.
Prototype : tout commence avec la conception
Durant environ les trois premiers mois du processus, la partie principale de cette longue route sera menée à bien. L'équipe de designers devra trouver de l’inspiration, adapter ses idées à l'identité de la ligne de design et tout traduire en un nouveau téléphone.
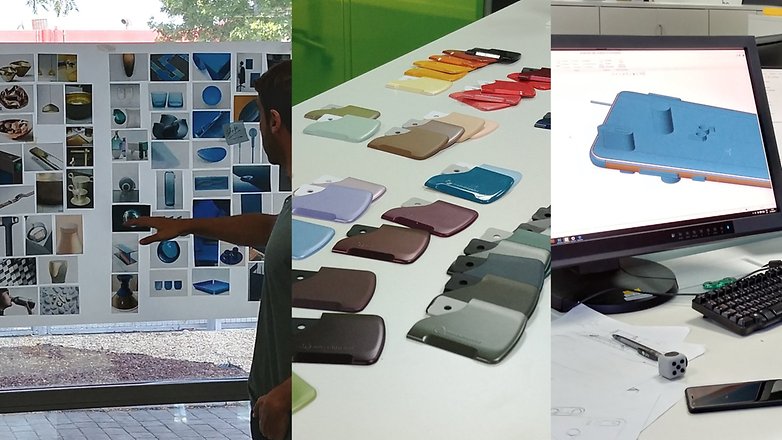
Comme on dit, « la pomme ne tombe jamais loin de l'arbre ». Si on regarde les appareils des trois dernières années de la marque espagnole (Aquaris E, Aquaris M et Aquaris X), le design a conservé sa personnalité, mais les détails ont profondément changé. Quelque chose que nous pouvons voir dans d'autres grandes marques comme Sony. Du Z1 au XZ Premium, les lignes ont été préservées, mais les détails font toute la différence.
Ceci, personnellement, me paraît être tout un défi pour les designers qui avec les mêmes lignes sont capables de créer une sensation complètement différente. Je suppose que le secret réside dans la façon de combiner élégamment des courbes avec des bords, des matériaux, des couleurs et des finitions. Avec les designs finaux, des maquettes en plastique sont préparées, qui ont le même poids que le dispositif final.
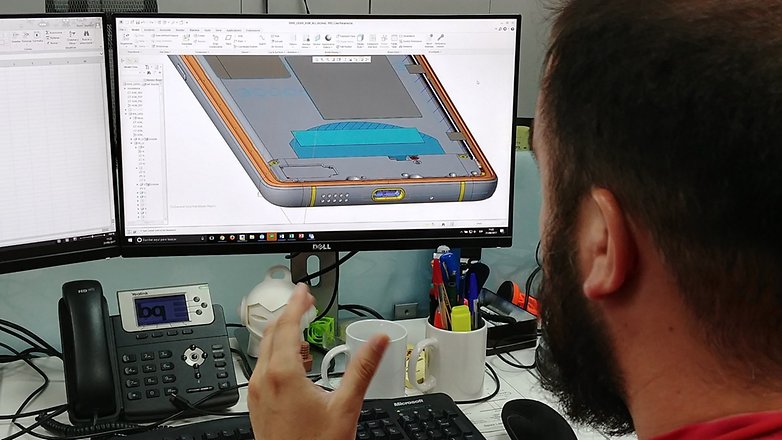
Une fois que nous avons une ébauche du design extérieur, c’est au tour des ingénieurs qui mettent tous les composants à leur place et qui les ajustent au dispositif. A ce stade, des composants aussi cruciaux que le processeur ou les modules de l’appareil photo sont sélectionnés. Grâce à un ordinateur, il est possible de réaliser une image virtuelle de l'ensemble du dispositif, y compris de son intérieur.
Les fabricants des divers composants tels que la batterie, le processeur ou les appareils photo disposent de pièces virtuelles de leurs composants, et de cette manière, il est possible de créer directement le dispositif à travers un écran d'ordinateur. En outre, des échantillons des composants sont disponibles afin de vérifier leur qualité et de se faire une idée de la façon dont ils peuvent s'intégrer en termes de qualité / prix dans le dispositif final.
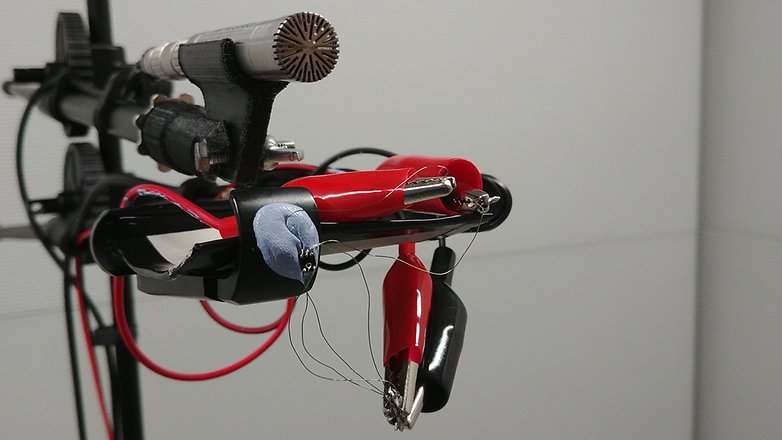
Un autre point essentiel de ce processus est la conception du PCB, la carte mère sur laquelle sont installés le processeur et les mémoires. C'est-à-dire là où toute la magie s’opère. La carte mère d'un smartphone occupe une place extrêmement réduite, et donc entre 8 et 10 circuits électroniques superposés relient toutes les pièces telles que les antennes, l'écran, les boutons, les appareils photo, etc.
Bien que nous avons décrit ce processus comme linéaire pour simplifier l'explication, il est en réalité beaucoup plus complexe. Le travail entre les différentes équipes est comme un match de tennis, qui s'échangent le design et modifient des parties ici et là.
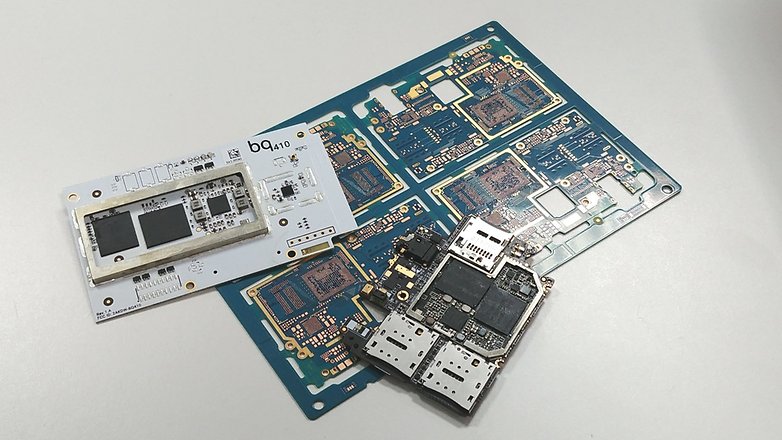
Le moment de vérité : les 80 premiers dispositifs
La deuxième étape du processus dure également environ trois mois et c’est quand les tests sérieux commencent. Davantage de groupes se joignent au développement comme celui du logiciel / firmware et de qualité. Les premiers appareils sont commandés à l’usine, environ 80 généralement pour commencer à tester la résistance, la connectivité, les performances et, bien sûr, pour commencer à préparer le logiciel qui équipera les dispositifs.
En ce qui concerne la conception, on teste que le dispositif est assez résistant pour survivre à nos vies trépidantes, et qu’il est également conforme aux normes de qualité de l'Union européenne. Pour cela, le processus est automatisé afin d'avoir des résultats mesurables. Plusieurs échantillons de la première série de dispositifs sont soumis à de nombreux tests de résistance physique tels que les chutes, la pression, les vibrations, l'intrusion de poussière, l'intrusion d'eau, le changement de température, et même la pression de notre derrière lorsqu’on s’assoit avec le smartphone dans la poche. Il existe une machine pour tout.
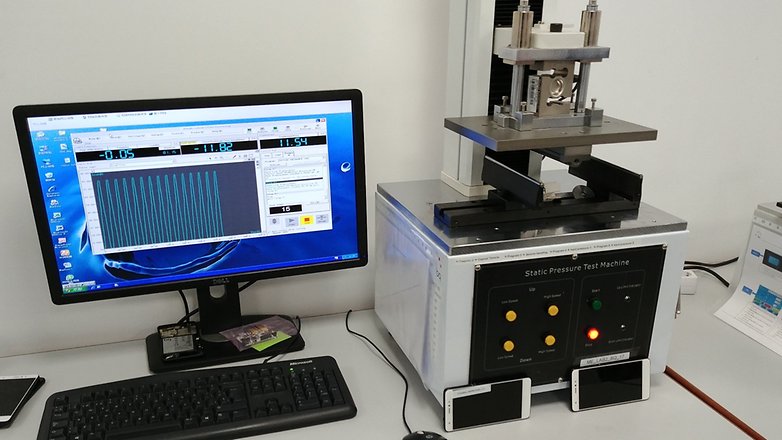
D’autres tests sont réalisés pour simuler les milliers de fois que nous touchons les boutons, ou les millions de fois que nous touchons l'écran. La qualité des composants incorporés dans le dispositif est testé, tels que l’écran, où on vérifie qu’il soit dans le bon ton de couleurs.
Il y a une autre catégorie de test des caractéristiques que nous ne voyons pas, mais qui affectent grandement l'expérience utilisateur. Pour commencer, il y a des tests thermiques. Après avoir effectué une étude approfondie des soudures, on observe comment le dispositif chauffe. Le système sur une puce (SOC), dans lequel est installé le processeur est la partie la plus chaude, et on observe comment la chaleur se dissipe à travers le dispositif dans le temps. A rendement maximal, ce n’est pas la même chose que la température monte à environ 40° en 1 minute qu'en 20 secondes. En si peu de temps, la main ne s’habituerait pas à cette augmentation de température.
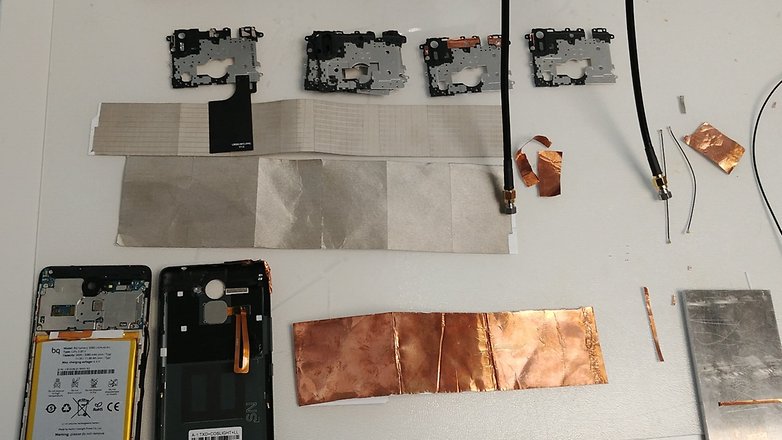
Chez BQ, la batterie compte sur sa propre équipe de tests. Il s’agit de l’un des éléments le plus important pour les utilisateurs, et il vaut donc la peine de s’y consacrer à fond. On teste également la position et la réception des antennes, en vérifiant que toutes les connexions (Wi-Fi, Bluetooth, LTE, 3G, GPRS, etc.) fonctionnent correctement.
Le son a également une équipe spéciale avec son propre équipement. Ce groupe d'ingénieurs, en plus de tester préalablement les composants qui seront montés sur le prototype, est également chargé de tester le résultat dans le dispositif et de configurer le logiciel afin que le son s'égalise de la meilleure façon possible en fonction de la situation. Pour tous ces tests, BQ dispose d’une chambre acoustique où faire ses tests et dans laquelle on ne peut tenir plus de deux minutes.
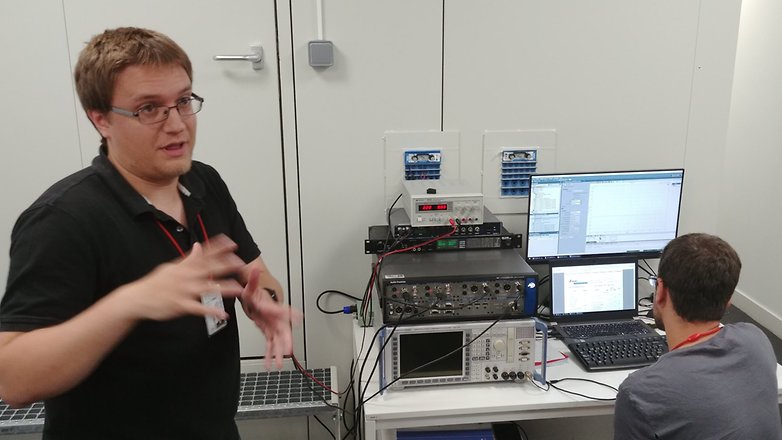
C’est ensuite au tour de l’appareil photo. Ce processus intègre une partie de test du hardware, mais la partie principale concerne le développement du logiciel qui contrôle le résultat de nos clichés. Pour ce faire, l'appareil photo est testé dans le laboratoire photo et le code est modifié jusqu'à obtenir les résultats recherchés. Les limites sont grandes parce que les capteurs de la caméra sont petits, la capacité de traitement n'est pas importante et les résultats doivent être immédiats.
Une fois que tous les contrôles sont effectués, que les changements nécessaires en termes de hardware ont été définis, et que le logiciel est presque prêt, il est le temps de commander les 140 premiers dispositifs de la version finale du dispositif.
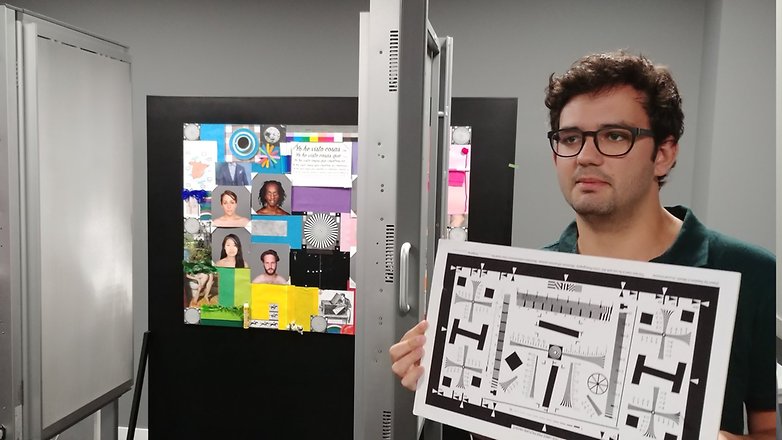
Tests finaux et production en masse du smartphone
Après la première phase de développement du dispositif et les tests des premiers prototypes, la troisième phase commence par la réalisation de davantage de tests de ces 140 prototypes qui ressemblent grandement à ceux qui seront mis en vente. Nous sommes au sixième mois de ce processus et tous les tests sont répétés sur les prototypes, et le logiciel du dispositif continue à être amélioré. Les changements de hardware ne sont en general plus d'actualité, à moins qu'un défaut soit découvert.
Une fois qu'il a été vérifié que tout le hardware fonctionne correctement et qu'il n'y a pas de problème, c’est le moment de faire un test de production de masse. Au cours du septième mois, nous passons à la quatrième phase, où une commande de plus de 2000 appareils est effectuée. Toute la batterie de tests sera également réalisée sur ces dispositifs pour vérifier que les smartphones produits en masse ont la même qualité que les prototypes testés précédemment.
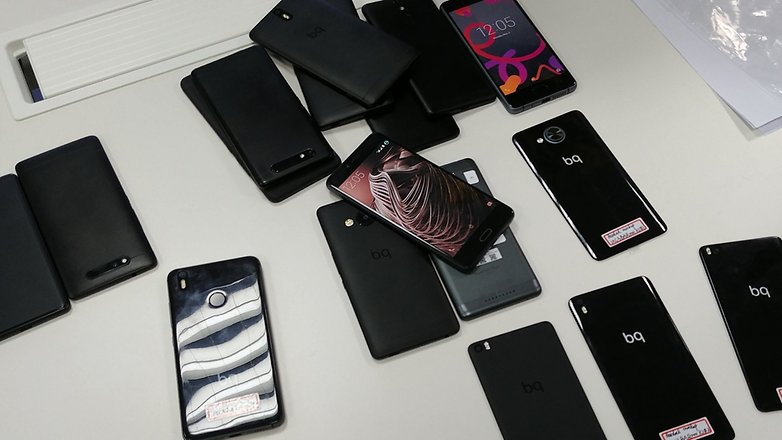
Lorsque tous les tests pertinents ont été effectués, le dispositif est prêt à être produit en masse, à partir d'environ un mois avant sa mise en vente. Jusqu'à cette date, l'équipe de développement peaufine les dernières fonctionnalités et le logiciel. Après neuf mois frénétiques, le smartphone arrive enfin dans les mains des utilisateurs, mais le fabricant ne cesse pas de s’en préoccuper. En ce qui concerne le hardware, le service technique prendra le témoin pour les réparations ou les remplacements de dispositifs. Et concernant le logiciel, l'équipe de développement continuera à travailler pour mettre à jour l'appareil avec des améliorations et des correctifs de sécurité, et l'adapter aux nouvelles versions d'Android.
Saviez-vous comment se fabriquait un smartphone ?
"Si on enlève les présentations et préparations commerciales, il ne reste qu’environ 9 mois pour développer une nouvelle série de téléphones pour l'année suivante."
Je doute que beaucoup de marques ne commencent à travailler sur la prochaine version seulement après la présentation de la précédente…
"les trois dernières années de la marque espagnole___ (Aqaris E,..."
A mon avis, il manque le principal : BQ !